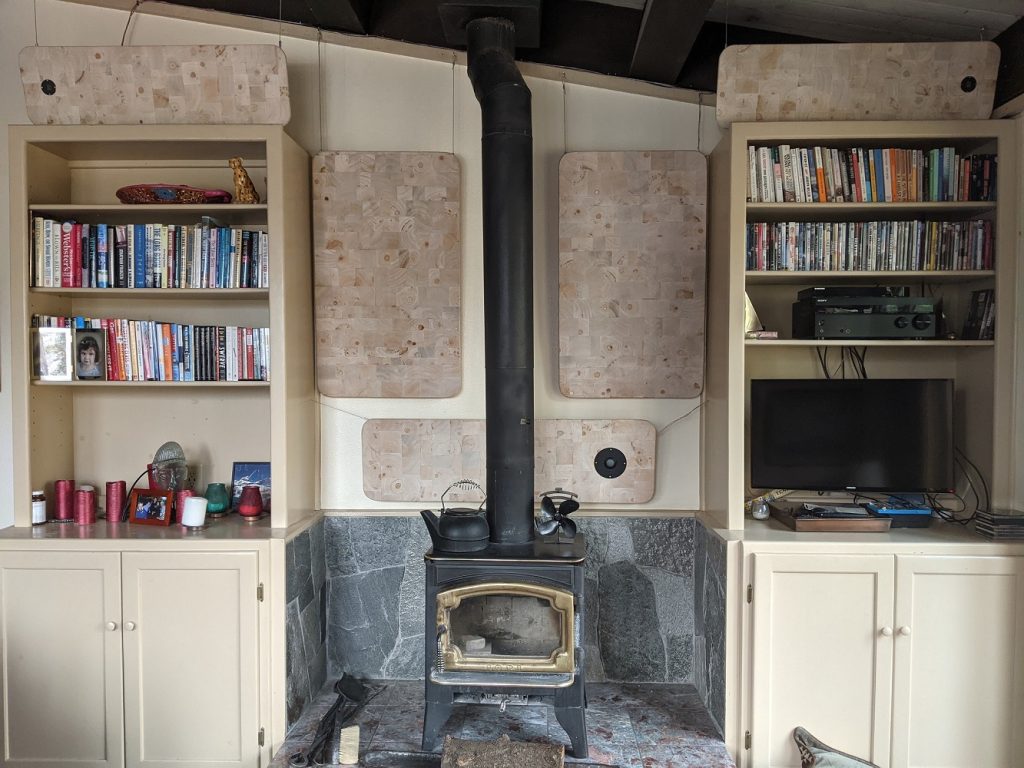
Alpine DML
Designer:
Bobby Kinstle
Project Category:
Freestyle Speakers
Project Level:
Intermediate
Project Time:
20+ Hours
Project Cost:
$500 – $1,000
Project Description:
This project was to create a nice sounding and aesthetically pleasing speaker system in an alpine vacation condo near Lake Tahoe that would be used mostly for classical or ambient music, and TV watching.
Design Goals:
It needed to blend into the existing room, connect to the existing amp, and play full range at moderate volume levels but not annoy the neighbors or the kid’s bedroom downstairs. It also needed to be 8 ohm and connect to the receiver already installed. The interior is wood themed so I opted to used end grain balsa rather than the usual foam core.
Driver Selection:
295-240 Dayton Audio DAEX30HESF-4 High Efficiency Steered Flux Exciter with Shielding 30mm 40W 4 Ohm. Two in series on each channel for 8 ohm load
264-1678 Peerless DA32TX00-08 1-1/4″ Corundum Dome Tweeter for the center channel tweeter because of it’s proximity to the fireplace I was concerned about heat on the AMT tweeters.
275-095 Dayton Audio AMT Mini-8 Air Motion Transformer Tweeter 8 Ohm
½” thick medium density end grain balsa sheet
Enclosure Design:
Each panel has a radius on the corner templated from a quart sized paint can to control unpleasant high frequencies. Each main channel consists of 2 panels. One wide panel with one exciter, one AMT tweeter, and the crossover. The second panel is larger and has one exciter to strengthen the lower midrange registers. The center channel is one large panel with the tweeter and crossover mounted to the edge closest to the TV. I plan on adding a second panel below it to strengthen the male vocals more to my liking. Wires, drivers, and components are generously secured with hot glue and solder joints are extra heavy since this is a high vibration environment.
Enclosure Assembly:
I glued small squares of hardwood to the corners of the panels for the eyelet screws to bite into securely and hung them from vinyl coated steel cables. Electrical connections zip tied to the cables helped conceal them. Each tweeter sat into a hole drilled into the panel and then filled with hot glue from the back side. The AMT tweeters were light enough they didn’t need additional support but the big Peerless dome screwed into a piece of wood glued on the back of the center channel. Wires were secured to the panels with hot glue.
Crossover Design:
All panels use 2nd order Linkwitz Riley crossovers for the exciters and tweeters. 2.1Khz on the center channel and 6Khz on the mains. All tweeters are wired reverse polarity. The preprinted Dayton 2nd order crossover PCB’s sure came in handy. I mounted the crossovers onto a thin piece of wood glued to the panel so the high mass components wouldn’t shake off. The center channel is crossed lower because I wanted it to be more directional towards the TV.
Tips & Tricks:
1. Vinyl coated steel cable is super strong, attractive to look at, can be made yourself in any length, and has no rattles whatsoever. Just make sure you strip the coating off underneath the crimp ferrule or it may slip out.
2. A glue injector is handy for filling in the cracks on balsa panels.
3. End grain balsa sounds fantastic but it’s mechanically poor. Screws won’t stay threaded into it. However, you can glue a 1/4″ thick piece of hardwood to it for heavy objects that need to be screwed down. The panel will break before that glue joint fails. This worked for threaded eyelets for the cables and as far as I can tell had no impact on sound quality.
4. DML panels make great midrange speakers with a range of around 120hz for big panels and 150hz for small panels to around 7ish Khz on the upper range. You are definitely going to need a woofer for them to sound right and it’s going to go high enough to be directional. Two small subwoofers mounted under the main panels would be ideal to play frequencies below 150hz. You can use a single sub but it will be directional in some frequencies.
5. AMT tweeters are spectacular for picking up the high end since they don’t weigh much, have stable impedance, and the smaller ones are really only good above 6K anyway. The Dayton AMT-mini-8 is super small and won’t change the sound of a large panel when mounted by an edge. It’s super crisp and blends very well with the panel.
6. Make sure you low pass the panel at the tweeter frequency as they can have some mighty unpleasant high frequency breakups.
7. Always mix at least 2 different sizes of panels on each channel. This blends the characteristics of the panels together in a pleasing way. I’m going to add a second panel under the center channel as the vocals feel a bit thin in home theater mode.
8. The VHB tape is holding so far but if it fails, most folks use epoxy to glue them back on.
9. While a multi channel amp, active crossovers, and a DSP can significantly “correct” the sound, I think chasing the usual goal of flat perfection will be and frustrating process. Instead embrace the beauty and character of the DML imperfections. Expect to listen and tweak before finalizing the project.
Conclusion:
When the music plays, the entire panel vibrates and acts like a giant speaker cone. This makes a huge sound field that swallows up the listener and mimics the sound of very large instruments like concert grand pianos that you just can’t replicate with small speakers. It sounds like the entire wall is playing music. Almost as if you were sitting in front of the band instead of through 2 distinct points trying to blend together. The huge surfaces replicate the fullness of large instruments like concert grand pianos, strings, and horns with a presence I’ve never heard from a speaker. The panels have their own character, and the sound is smoother and mellower than most speakers. Adding the AMT tweeters brought the crisp details back in and contribute to a truly enjoyable experience. The bass comes from the end table subwoofer I posted earlier and has no trouble filling the room with lots of deep bass. Best of all the subwoofer is hardly audible in the bedroom below this room thanks to it’s non resonant chassis and spiked isolation feet.
Sip your favorite spirit and relax to something classical.
About the Designer:
I grew up in the Mojave Desert in a small community of scientists, craftsmen, and engineers. We were the kind of people who didn’t accept “it’s impossible” or “you can’t do that”. If I want something that doesn’t exist, I’ll just make one. Now I’m a thermal engineer in the computer industry and I currently hold 17 patents worldwide.
Project Parts List:
Part # |
Description |
Qty |
264-1678 |
Peerless DA32TX00-08 1-1/4″ Corundum Dome |
1 |
275-095 |
Dayton Audio AMT Mini-8 Air Motion Transformer Tweeter 8 Ohm |
2 |
295-240 |
Dayton Audio DAEX30HESF-4 High Efficiency Steered Flux Exciter with Shielding 30mm 40W 4 Ohm |
6 |
266-830 |
ERSE 1.3mH 18 AWG Perfect Layer Inductor Crossover Coil |
2 |
027-114 |
Audyn Cap Q4 4.7uF 400V MKP Metalized Polypropylene Foil Crossover Capacitor |
2 |
260-130 |
Crossover PC Board 2-Way 12 dB |
3 |
257-032 |
Dayton Audio 0.40mH 20 AWG Air Core Inductor Crossover Coil |
4 |
027-212 |
Dayton Audio PMPC-1.5 1.5uF 250V Precision Audio Capacitor |
4 |
N/A |
½” thick medium density end grain balsa sheet 24×48 |
5 |
N/A |
#8 threaded eyelets |
1 |
N/A |
3/32 vinyl coated steel cable |
1 |
N/A |
Hot glue |
1 |
I truly appreciate your humble, elementary manner of explaining exactly what considerations led to the various decisions made in both the conceptualization and implementation of what appears to be a well thought out response to a well thought out, ambitious goal. Aesthetically, ergonomically, and based upon the stated conclusion, acoustically satisfying…… simultaneously satisfying the required capability for A/V use &, I’m assuming most challenging, the desired response to a musical genre that is by no means forgiving. (My personal audio ambitions consistently prioritize analog reproduction of music, with “home theatre” of far less a concern; I mention this only to disclose my preconceived notions about what aspects of such a design would be most challenging to attain. Other than a shared appreciation for building what I want instead of paying a small fortune for the closest fit, I’d be willing to assume that your wealth of knowledge is exponentially greater than mine; a point that only further demonstrates the articulate nature of your ability to educate others. And, if I know anything, it’s that one’s ability to convey knowledge is the most appreciated attribute. Thank You!
Nick
Thanks for your generous compliment Nick. To be honest, I was utterly terrified through most of the project that it wouldn’t work. I’ve built a few speakers and found that following the standard rules with good quality parts will usually get you pretty darn close to ideal performance. That is, I’ve never built a bad sounding speaker by following the points above. However DML is so far off the reservation that most of the standard rules didn’t apply. I decided that the best approach would be to make panels of different sizes to blend their characteristics together. I did play around with the technology as part of a mad science project at work that didn’t go anywhere and one thing that I noticed was almost any panel had some unpleasant characteristic about it, but mixing panels solved the problem pretty well. Perhaps DML can’t produce a world class Merlot, but it can produce a really amazing red blend. I think the highly variable and random density of the end grain balsa also helped with that problem.
When I demoed the system to it’s new owners one of them played some Glenn Gould for a while. He sat on the edge of the couch with his eyes half closed. When it was over he turned to me and said “There are two things here I have never heard in any speaker except headphones. First, I can tell the difference between a grand piano and a concert grand. The second is this is the only time I could hear Glenn Gould’s fingers dragging off the keys.” When he said that, I knew I had hit a home run. It was like he’d removed a 50 pound weight from my chest. After that we poured some wine and poured through his music collection until the wee hours of the morning.
This weekend I added a second, larger panel underneath the center channel panel. Perhaps due to the huge mass of that Peerless tweeter and it’s large crossover inductors, I felt the center channel sounded a little thin, especially on male voices despite having two exciters. The second panel was the same width, but about 30% taller. This really improved the fullness of the center channel audio. Also increased the output by 3db. The exciters both fell off the center channel after it was accidentally dropped, so I moved one exciter to the second panel and kept the series wiring. The epoxy won’t fall off that’s for sure. So far none of the other exciters have fallen off. I also got to see how much the fireplace was heating up the components and in reality, the surface were barely warm to the touch. Seems I worried way too much about that.
I appreciated the write-up details. Thank you for the comments on the overall panel response. Just need to get off my ass and complete a DML center channel for my Rhino_20 array ( Don Keele design based on rock solid Sonar beam forming )
Jim Morton, retired CPU design engr.
Look into Synthetic jet impingement cooling, very efficient for heat transfer
When making a center channel DML try to make it a little bit more square-ish than the long wide format is usually standard for center channels. A 3’x2′ pannel will do really well for male voices for example. But a panel that’s only 12 to 14 in tall and very wide will sound a little thin.
Being a fellow Californian, it crossed my mind that having (very) low-mass speakers on cables is a good safety measure for high-wall applications in earthquake prone regions.
Good point. If these come down in an earthquake, it’s because the walls came down. Plus they would move during minor quakes giving a visual indication that an earthquake occurred.